0066// Fabrication process selection for high precision controlled profile?
- Guan Boon, Wong
- Nov 18, 2016
- 2 min read

(Photograph courtesy of Hypertherm)
There are different types of fabrication process available in the market for high precision profile control. Since, high/low is a relative adjective. Therefore, just to keep everybody in the same page. The high precision we discuss here is <50 micron positional controlled tolerance zone or <5 micron form control.
There are few things need to take note when selecting a "best fit " process for your design.
1. Functional requirement (always the top factor affect your design in GD&T perspective.)
2. Acceptable deviated profile
(These factors are chosen based on my experience only, may have other important selection criterion may not cover here. Key word here, functional requirement !!! )
Functional requirement
Functional requirement always the most important factor affecting your design, process and quality control. Therefore, first thing before you start anything, understand the functional requirement for that interested surface profile.
Example of functional requirement:
1. Mating surface
2. Locating surface (position or orientation)
3. Datum establishment surface for assembly
4. Cosmetic surface
5. Electric/Magnetic field generating surface
6. Heat transfer surface
5. Absorption surface (chemically or physically)
6. Abrasive surface
7. Surface for secondary process (e.g. coating)
8. etc
Acceptable deviated profile
Different functional requirement required different type of surfaces. For example, when you choosing fabrication process for a locating surface which shown in diagram below, etching may not a good choice for you, because wear and tear due to damage of feather may cause the surface lost its locating function.

In some of the application, roughness for the surface is an important factor. Secondary process such as reaming or electropolishing will help to reduce the roughness of the surfaces.
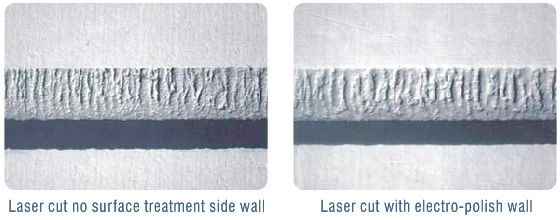
(Photograph courtesy of QualiEco Circuit Ltd.)
Besides that, burr free can achieve by etching, deburring, tumbling, electropolishing and etc. But, in some circumstances, these processes are not allow. OR that particular surface not allowed to have any secondary process due to chemical composition requirement of that particular surface. Therefore, by adjusting the fabrication parameters, this can help you achieve the desired profile too. For example, by adjusting speed for plasma arc cutting's speed to optimum window, it can help to reduce dross (it look like burr for layman =D).

(Top: Optimum speed; Middle: Too fast! ; Bottom: Too slow! ; Photograph courtesy of Hypertherm)
Therefore, discuss with the vendor to understand their capability can help you choose the right process!
return 0;
Comments